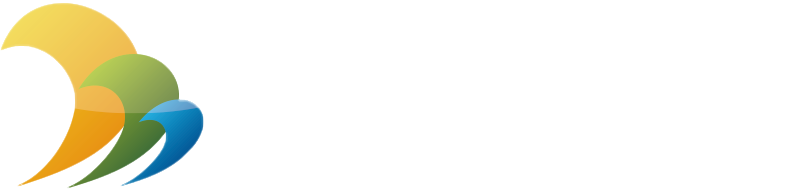
弱市之下 建模助力船企转型升级
“不接单是等死、接单是找死”是经济下行期船企难以回避的尴尬。为此,工业和信息化部在日前召开的推进全面建立现代造船模式的宣贯会上提出“切莫放松建模工作”,这为处在转型升级关键时期的船舶工业指明了道路。
见贤者思齐
有关船企建模的必要性,统计数据或者更能让人一目了然:国内某先进船厂每修正总吨工时为22.9,而韩国现代重工则只要16.7,日本三井造船仅有8.1。我国船企的建造效率与日韩企业相比,仍然存在较大差距。
对此,业内专家表示,每造一艘船需要消耗上百万个工时,如果单纯依靠人工调度,就永远是落后的造船模式,我国船企还需深入学习以日韩等先进船舶工业国家为代表的现代造船模式。
所谓现代造船模式,是以统筹优化理论为指导,应用成组技术原理,以中间产品为导向,按区域组织生产,壳舾涂作业在空间上分道,时间上有序,实现设计、生产、管理一体化,均衡、连续地总装造船。换言之,就是指以高度总装化为特征、以精益生产为核心的造船模式,其精髓是消除生产过程中的一切浪费,追求精益求精和设备、工时、物料的精细计划与控制。
“日本的造船企业,能把一年的计划安排到月、周、日、甚至小时。”中国船舶工业行业协会会长张广钦表示,这就是因为企业通过日积月累的统计,将每个工作岗位、每个工人和他们每天的作业内容和消耗记录下来并录入计算机系统,通过基础的原始积累,加上优化分析进行数字化造船的实践。
具体而说,现代造船模式,是把建造一条船需要的所有资源,全部用计算机优化设计多次,将场地、设备材料的纳期,各工种人员的调配都纳入计划并及时调整不合理之处,既避免了无谓的浪费,又使信息化和工业化生产高度融合,使等工、返工和到处跑的现象锐减,同时也不需要以拖延工作时间来完成工作量,这一切都得益于精细化管理而完成。
反观我国船企,经过多年努力,虽然造船周期大幅缩短,生产线布置更加合理,硬件方面已经与日韩船企相差无几,但管理粗放,基础薄弱的状况长期以来并未得到改观。计划欠缺精细考量,物流与生产流畅难以同步,这或许在船价高企足以确保较大利润时尚能维持盈利,而在如今市场普遍低迷之下,千里之堤也可能溃于蚁穴,建模工作或将关系着企业的生死存亡。
建立高效船舶制造体系
对比国内外造船模式的实践,我们可以发现,建模是船企提升生产效率的最有效手段。事实上,我国船企开展建模工作已有30年之久。自上世纪80年代初至今,尤其是《国防科工委关于加快建立现代造船模式的指导意见》和《全面建立现代造船模式行动纲要(2006-2010年)》发布以来,我国船舶工业的建模工作已经取得显著成效,骨干企业基本建立起以中间产品组织生产为基本特征的总装造船模式。
建模是新时期船企转型升级的必由之路。2012年,工信部曾先后颁布了《推进全面建立现代造船模式工作指导意见》(以下简称《意见》)和《船舶建造技术水平评估方法》,提出船舶行业及企业必须将建模作为转变行业发展方式的突破口,推进建模工作在深度、广度和精度三方面进入全面提升的新阶段。
《意见》提出,2015年的建模工作目标是全行业基本建立高效船舶制造体系,主要造船技术指标接近国际先进水平;全员劳动生产率年均提高15%,骨干造船企业造船效率达到15工时/修正总吨,典型船舶建造周期达到世界先进水平,骨干造船企业平均钢材一次利用率达到90%以上,规模以上企业单位工业增加值能耗比“十一五”末下降20%;大中型企业造船管理信息化普及率达到80%,数字化设计工具普及率达到85%。
为推荐船企建模工作的全面开展,工信部和中国船舶工业行业协会日前共同举办了《推进全面建立现代造船模式工作指导意见》和《船舶建造技术水平评估方法》宣贯会议。
“建立现代造船模式,可以使企业根据实际情况检验生产流程是否合理,生产组织是否有扯皮推诿现象,生产准备是否到位,各工种劳动力配备是否满足。”张广钦认为,建模工作的意义在于运用先进的计算机技术改变原先传统的落后的管理模式,把整个企业的产品生产所需要的信息流、物流、资金流以及劳动增值流都纳入集中地、精确的计算机计划管理渠道,以减少各种无价值的浪费。
把握机遇推进建模
接单难、交船难、融资难、盈利难,这横亘在船企面前的“四难”如今让多数船企焦头烂额。有业内人士表示,此时推动建模,可能会给船企加重负担。这样的顾虑虽然不无道理,但从长远来看,以建模工作促转型升级才是保持船企持久生命力的源泉。
时下,持续低迷的船市和不断上升的劳动力成本让“家族式”管理模式和“作坊式”无坞造船的弊端日益凸显,“不计成本投入换产出”的套路已被证实行不通,建模工作从未像今天这样重要。