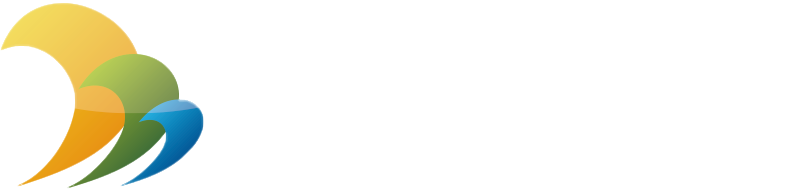
产需对接 让船配业升级少走弯路
我国船配业有望再修复一个Bug(故障)。
液化气船是双燃料发动机的使用大户,我国船厂对该船型积累了丰富的建造经验,近两年,国内主机厂商也纷纷引进双燃料发动机专利并投入生产。不过,为发动机供气的双壁管一直以来都是国内船配业的一根“软肋”,长期被以韩国为首的国外供货商所垄断。好消息是,本报记者从国内某船管生产企业了解到,该公司已成功研制高压双壁管,攻克了该型管在材料、关健零部件等方面的核心技术,并已投产。
该船管企业一年来的研发之路走得艰辛,不过该公司与船厂需求的“无缝对接”,也保障了整个项目能够披荆斩棘、开花结果。今年3月,工业和信息化部印发《船舶配套产业能力提升行动计划(2016~2020年)》,其中提出,要促进产需对接,鼓励船舶配套企业联合船东、船厂、船舶设计单位、高校、研究机构等建立产业创新联盟,开展产业协同创新、协同制造。我国船配业的升级绝非只有“华山一条路”,不过在行业形势不明朗的当下,国内众多配套企业能够进一步对接用户需求、优化研发资源,着眼细节逐步发力,不失为船配企业走出困境、提升能力的一条“弯路少”、成本低的上乘策略。
发挥生产优势 突破薄弱环节
虽然我国船舶配套业总体层级较低,不过国内工业基础较好,不少加工生产能力强的企业如果找对了方向,是完全有能力在一些高附加值船配产品上率先取得突破的。高压双壁管的研制就是一个典型的例子,虽然在选材上颇费了一番周折,但企业在设计、生产、精细管理等方面,都有能力媲美韩国企业。
据了解,高压双壁管由三部分构成——内管、外管以及起到内外管固定作用的弹性支架,弹性支架是高压双壁管的核心技术。一般而言,一艘中小型液化气船需要70多个弹性支架用于内外管的固定,每一个弹性支架由金属材料和耐磨材料两部分构成。船舶寿命以20年计,两管之间的弹性支架需要承受长时间的主机振动和相关磨损,因此,对材料的要求非常苛刻。
目前,国内尚无合适的金属材料用于弹性支架,这给企业的研发带来了很大的麻烦。据悉,该船管企业先后联系了国内15个厂家,尝试了301、304、316L等不同型号、不同厚度的钢材,在材料研究所做了4次刚度试验和位移疲劳试验,但都不能满足技术要求。国内的钢材找不到,企业开始寻找国外厂商,终于得偿所愿。据了解,该特种钢材的硬度极大,一般的剪刀车无法作业,只能用激光切割,并要经过多套特制磨具进行十几道压制工序加工成型。
双壁管质量的核心是精度。此前有消息称,韩国的双壁管制造商也出现了质量不合格的情况,问题就出在双壁管的同心度、弹性支架的安装角度上,这在进口材料中非常罕见,高压双壁管的生产难度可见一斑。为了满足内外管同心度以及弹性支架的安装要求,国内这家船管企业对内外管尺寸、弯管过程都进行严格的精度控制,对每一段船管进行单独的尺寸计算。该公司还专门设立了工艺工序控制点和质量检验点,采用测厚仪、扭力显示扳手、角度测量尺等专用设备和工具,确保高压双壁管的质量以及装配精度。
分散成本压力 优化整合资源
不仅是在船管领域,今年国内船企与院校、配套商甚至跨行业公司的合作,都迸发出不少火花。例如,由山东硕力机械制造有限公司、武汉理工大学、江南造船(集团)有限责任公司三方,产、研、用通力合作的产品6000吨级“SKWB-2500船舶大型三维数控弯板机”就在江南造船成功应用。该产品能够根据造船软件系统提供的船板加工数据,使用专业计算和控制软件,自动进行曲面造型和三维曲面船板成形加工,使三维曲面船体外板冷压及自动成形的世界性技术难题得到基本解决。江南造船负责人介绍,该型弯板机一改以往由老师傅凭经验生产的历史,进一步提升了生产效率和质量。在上海外高桥造船有限公司,本报已多次报道了其与沈阳新松机器人自动化股份有限公司在船舶喷涂机器人方面的合作。
以上的这些案例,都是由国内骨干船厂牵头,联合各界的研发力量,这些项目更贴近一线需求,在应用开发、产品市场等方面,也就具备了先天优势。
研发成本是企业绕不开的问题,特别是在当前行业形势不明朗的情况下,除了能够争取到的国家各项科研经费之外,企业很多时候还需要进一步投入资金。对于单一的研发主体而言,这是不小的压力,也增加了企业研发的不确定性。曾有压载水处理系统的供货商向记者介绍,其所在的公司内部,就在是否进一步投入上千万元资金进行设备的升级换代这一问题上出现了分歧。产需结合、联合多个研发主体,是分散成本压力、优化资源的一种不错的解决方法。数据显示,高压双壁管的国产化能够给企业节省50%以上的购入成本。