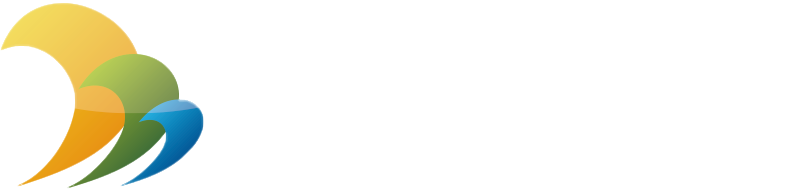
中国船配业加速“弯道超车”
随着供给侧改革和产业结构优化,中国船舶制造产业迎来了产业升级的机遇。在行业政策和市场需求的驱动下,船型升级、行业整合以及配套设备行业的发展正改变着中国船舶制造产业的结构与格局。
日前,工业和信息化部、国防科工局印发《推进船舶总装建造智能化转型行动计划(2019-2021年)》(以下简称《行动计划》)的通知,船舶配套设备行业作为船舶产业价值链中的重要一环,又将迎来怎样的发展?
“巨轮之芯”中国造
大型船用曲轴是万吨轮最重要的核心装备,被誉为“巨轮之芯”。是否具备大型曲轴制造能力,是衡量一个国家造船工业水平的重要标志。
2018年12月15日,全球首支22000TEU集装箱船船用曲轴(W12X92型)成功下线。该船用曲轴由大连华锐重工集团股份有限公司所属大连华锐船用曲轴有限公司(以下简称“大连华锐曲轴”)研制,通过WinGD公司、法国船级社(BV)、上海中船三井造船柴油机有限公司的最终联检,将安装在22000TEU超大型集装箱船的发动机上。
W12X92型船用曲轴采用对接式结构,总长度为23.519米,重量达到488吨,在全球尚属首次研制。由于此前没有任何参考资料,所以该型船用曲轴的研制难度较大。为此,大连华锐曲轴加大资金投入,升级改造加工设备,创新加工工艺工法,改进刀具选用流程,最终解决了热装精度、曲拐加工回转直径超限等5项技术难题,确保产品的所有检测数据全部满足质量规范和图纸要求。
“该型船用曲轴成功下线,将助力大连华锐曲轴在与国内外同行的试制竞赛中取得优势。”大连华锐曲轴有关负责人表示,W12X92型曲轴是大连华锐曲轴立足于“高端制造、世界一流”发展战略、加快产品结构调整取得的又一重要成果,是继成功研制国内首支曼能源解决方案公司系列特大对接11S90ME-C型曲轴、G80型曲轴和瓦锡兰系列82T型曲轴之后,该公司在超大型低速船用柴油机用曲轴制造领域的又一次重大突破,填补了世界空白,标志着大连华锐曲轴成功跻身世界超大型船用曲轴制造行业前列,让“船等机、机等轴”制约国家造船业发展的瓶颈成为历史。
2018年12月13日,由武汉重工研制的国内首件超长空心桨轴顺利交付并得到客户好评。此件螺旋桨轴长约22.5米,重约20吨,是武汉重工承接的空心细长轴类产品中最长的一件,也是国内第一件。自接到订单后,公司上下高度重视,技术人员共同研究探讨,制定多项工艺方案。从锻造、热处理到机加工的深孔、外圆、法兰孔加工,直至最后的包装、发货,所有流程精益求精,过程控制严格,确保产品质量。
克服“成长的烦恼”
如果说2002年前,我国船舶配套合资企业还都是零星成立的话,那么,随着2002年后全球船舶行业进入快速发展阶段、造船业向中国转移态势明显,我国的船舶配套合资企业如雨后春笋般涌现。齐耀瓦锡兰菱重麟山船用柴油机有限公司、丹柯斯船用系统(上海)有限公司、重庆ABB江津涡轮增压器有限公司、瓦锡兰推进装置(无锡)有限公司、安特优发动机工程(苏州)有限公司、上海中船三井造船柴油机有限公司等一批较大型船舶配套合资企业纷纷成立,涉及柴油机、辅机、发电机组、推进器、螺旋桨、重型吊装设备、控制系统、消防系统、舱室机械等多种产品。
目前,船舶设备制造业的高端产品和品牌仍然集中在挪威德国等欧洲造船强国和日韩,中国的船舶配套产业尚处在成长阶段,进口依赖程度较高。其中,高端柴油机、推进系统和通讯导航设备是国产替代潜力较大的几个领域。
近年来,为了弥补船舶产业的短板,更好地满足航运与造船业的需求,中国造船和配套企业在产业政策的引导下,通过技术引进与合作、自主研发等方式,不断提高配套设备研发与制造能力,关键设备领域的国产化率也在稳步提升。
在动力系统领域,国产的低速、中速和高速柴油机均取得了突破并获得了市场认可;在环保设备领域,青岛双瑞成为全球首家获得IMO新G8型式认证的船用脱硫洗涤设备供应商,其BalClor系列压载水(产品推荐)管理系统成为亚洲首家获得美国海岸警卫队(USCG)认证的压载水处理设备。
2012年,南通中远海运川崎提出将智能造船作为转型升级的主攻方向和实现造船强厂目标的主要途径,并开始布局第一条型钢智能生产线。截至2017年,南通中远海运川崎已经拥有条材焊接机器人生产线、先行小组焊接机器人生产线、小组材焊接机器人生产线等在内的近20条自动化生产流水线,内业智能车间、管子智能车间在内的5个智能车间。自智能生产线投产以来,应用总体成效显著,相关工序生产效率提高了2-4倍。
还有,武汉船机“船海工程机电设备数字化车间”以调距桨产品为突破,率先部署有生产数据采集设备,通过智能加工单元、智能装配单元以及智能焊接单元,实现关键加工过程的智能化,从而提高加工精度、效率及质量;重庆红江“船用柴油机核心部件数字化车间试点示范”入围工信部2017年智能制造试点示范项目名单;大连中远海运川崎引入国内首条世界领先的船用钢板信息智能录入流水线,其“船舶智能制造示范”项目入围工信部2018年智能制造试点示范项目和人工智能应用试点示范项目名单……
越来越多的我国众多骨干船企和船配企业扩大规模、提升技术,将自主创新和推进智能制造作为企业加快转型发展的重要方向。
智能升级勇闯新路
《行动计划》明确指出,经过三年努力,我国船舶智能制造技术创新体系和标准体系初步建立,切割、成形、焊接和涂装等脏险难作业过程劳动强度大幅降低,作业人员明显减少,造船企业管理精细化和信息集成化水平显著提高,2-3家标杆企业率先建成若干具有国际先进水平的智能单元、智能生产线和智能化车间,骨干企业基本实现数字化造船,实现每修正总吨工时消耗降低20%以上,单位修正总吨综合能耗降低10%,建造质量与效率达到国际先进水平,为建设智能船厂奠定坚实基础。
近日,工业和信息化部、交通运输部、国防科工局也联合印发《智能船舶发展行动计划(2019-2021年)》,提出围绕智能船舶辅助决策、自主控制等功能需求,系统梳理感知与控制基础元器件技术要求,着重补齐短板,强化综合集成。推动船舶航行、作业、动力等相关设备的智能化升级,研制信息和控制高度集成的新型船用设备,全面提升船舶智能化水平。
随着新一代信息通信技术的快速发展,数字化、网络化、智能化日益成为未来制造业发展的主要趋势,世界主要造船国家纷纷加快智能制造步伐。船舶制造是典型的离散型生产,由于船厂空间尺度大、船舶建造周期相对较长、工艺流程复杂、单件小批量、中间产品种类非标件数量多、物理尺寸差异大、作业环境相对恶劣,对数字化、网络化、智能化技术应用提出了特殊要求。
21世纪以来,我国船舶工业实现了快速发展,骨干造船企业建立起以中间产品组织生产为特征的现代总装造船模式,并不同程度开展了智能化转型探索工作,取得了一定成效。但是,总体上我国船舶制造业仍处于数字化制造起步阶段,而且各造船企业发展水平参差不齐,三维数字化工艺设计能力严重不足,关键工艺环节仍以机械化、半自动化装备为主,基础数据缺乏积累、信息集成化水平低等突出问题亟待解决。
《行动计划》提出,我国船舶工业正处在由大到强转变的战略关口,造船企业应在全面建立现代造船模式基础上,把握机遇,顺应趋势,主动作为,努力赶超,推动我国船舶总装建造智能化水平迈上新台阶。
智能船舶研制是一个循序渐进的过程,任何时期都离不开智能船用设备的支持,但不同时期对智能船用设备的要求又是不一样的。智能制造装备实现高效运用是船舶、船配企业持续推进智能制造的重要动力,而精益设计、精益生产、精益管理和信息技术大数据平台是智能制造装备充分发挥效率、实现能力的重要支撑。
习近平总书记多次强调,“改革开放只有进行时、没有完成时”。经过改革开放40年的发展,我国已经是名副其实的世界造船大国,但还不是世界造船强国。从造船大国迈向造船强国,我国船配业仍需苦练内功,加强创新,勇闯智能升级新时代!